Industrial operations
Bracell has a production capacity of 500,000 tons of special cellulose per year in Bahia and 250,000 tons of kraft pulp per year in São Paulo. Our factories use a highly-advanced production process to obtain high levels of purity, with an alpha-cellulose content of up to 98.5%.

Supply
The eucalyptus arrives at the factory and is temporarily stored in the wood yards.
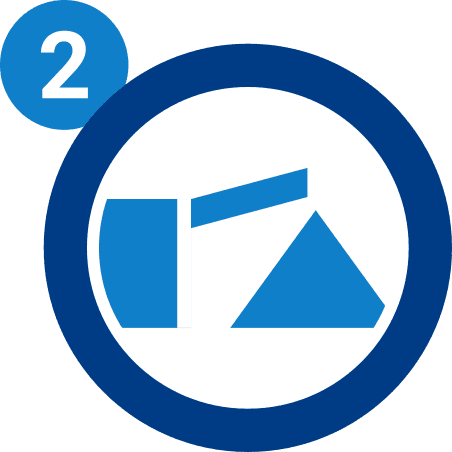
Wood chipping
The logs are washed and chopped into small pieces known as chips.
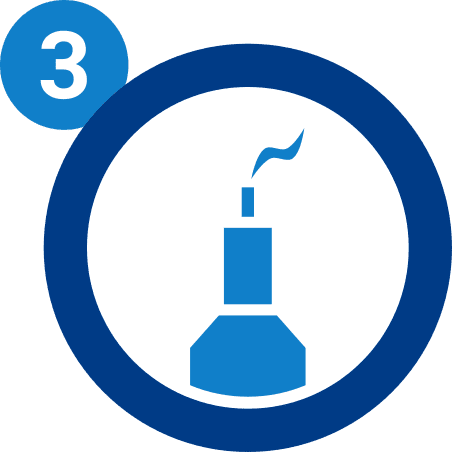
Cooking
The chips are cooked in the digester, where separation of the wood fibers occurs. These fibers form the brown cellulose pulp.
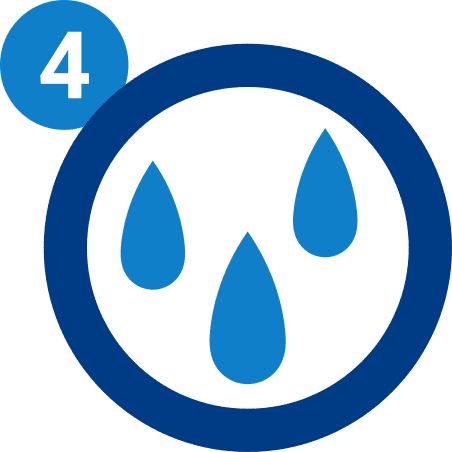
Washing and depuration
After cooking, the chips that were not fully cooked are separated and the brown cellulose is washed. A by-product obtained from the washing of the cellulose pulp is black liquor, which contains the dissolved organic solids of the wood and the chemicals used in cooking.
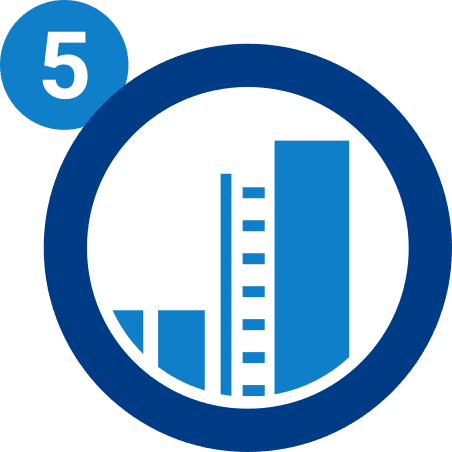
Recovery
The black liquor originating in the wash is evaporated and used to generate steam, producing the electricity needed to power the mill. This process also allows 98 per cent of the chemicals from the production of cellulose to be reused.
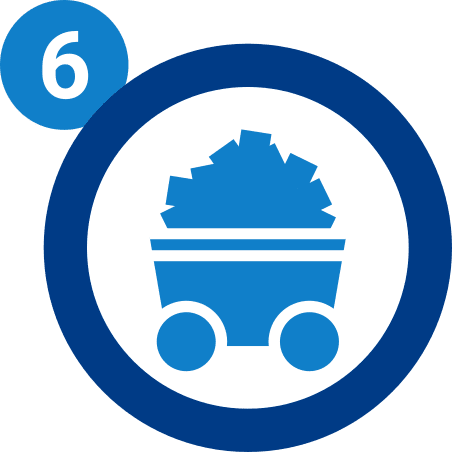
Cold alkaline extraction
The final step of the washing and scrubbing process comprises cold alkaline extraction, which increases the purity of the cellulose.
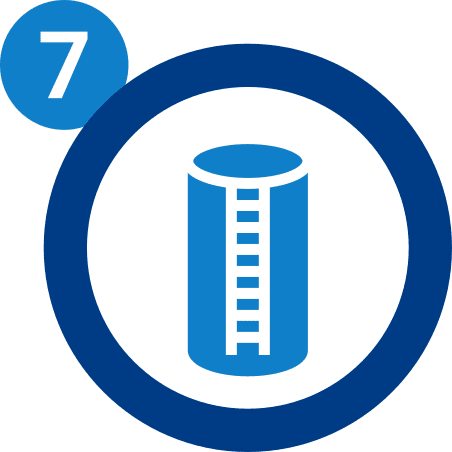
Bleaching
After cleaning and washing the brown pulp, it is treated with chemicals.
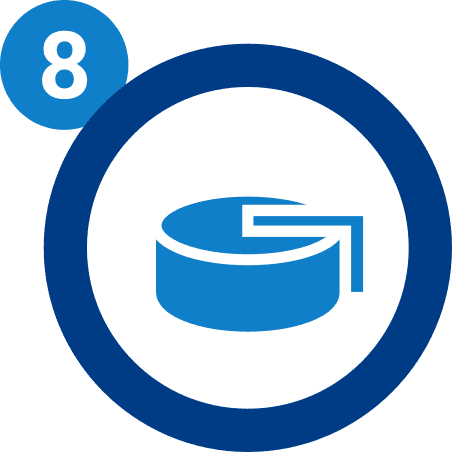
Waste and effluents
Much of the solid waste from the production process is recycled.
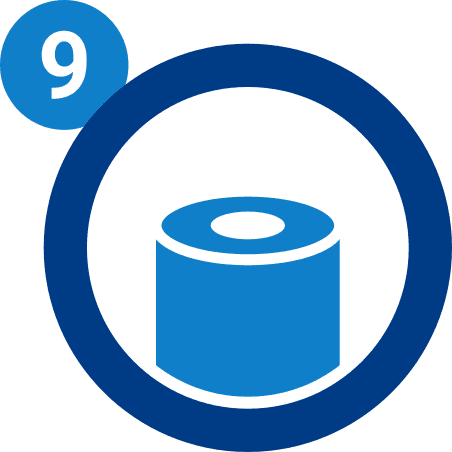
Drying and packaging
After bleaching, the cellulose is pressed into sheets and dried with hot air. The dried sheets are cut and packaged in bales or reels, according to the customer’s need, and stored.
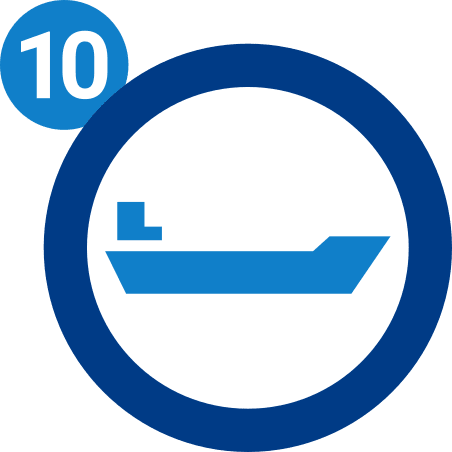
Final destination
From the warehouse, the product is sent on to customers.